Various Machinery Types for Processing Natural Stone
Various Machinery Types Natural stone processing involves a meticulous and intricate process that requires specialized machinery to achieve precision and efficiency. Granite factories utilize a range of equipment to cut, shape, and finish stone for various construction and decorative purposes. Curious about the machinery involved in natural stone processing? Here's an overview of the key tools used in granite manufacturing. The choice of machinery also reflects the increasing demand for sustainability and precision. Automatic slab polishers optimize the polishing process, reducing waste while ensuring a uniform finish. Calibration machines ensure that tiles and slabs are perfectly leveled, making them ready for installation with minimal effort. Together, these tools demonstrate the technological advancements that have revolutionized the granite manufacturing industry, making natural stone more accessible, versatile, and efficient for various applications.
What is Granite Manufacturing?
Granite, a natural stone, is extracted from the earth in large blocks. However, these blocks are not ready for direct use in construction projects. They must undergo several processes to be cut into specific sizes, polished, finished, and shaped. This is where the importance of advanced machinery comes in.
Granite manufacturers, such as Regatta Granites India, play a significant role in this process. With in-house manufacturing units in North and South India, they possess the capabilities to process granite efficiently. Let's delve into the essential machinery used in granite processing.
1. Jumbo Granite Gangsaw
As the name suggests, this machine is designed to cut massive granite blocks into gangsaw slabs. A Jumbo Granite Gangsaw is a heavy-duty machine that operates with high precision. Granite blocks are positioned on a platform, which moves beneath a fast-running blade to create slabs.
Also known as a diamond row saw or granite frame saw, this equipment uses multiple diamond saw blades, typically ranging from 60 to 120, to ensure straight cuts, superior quality, and optimized output. Despite its high cost and complex installation, it is indispensable for large-scale granite processing.
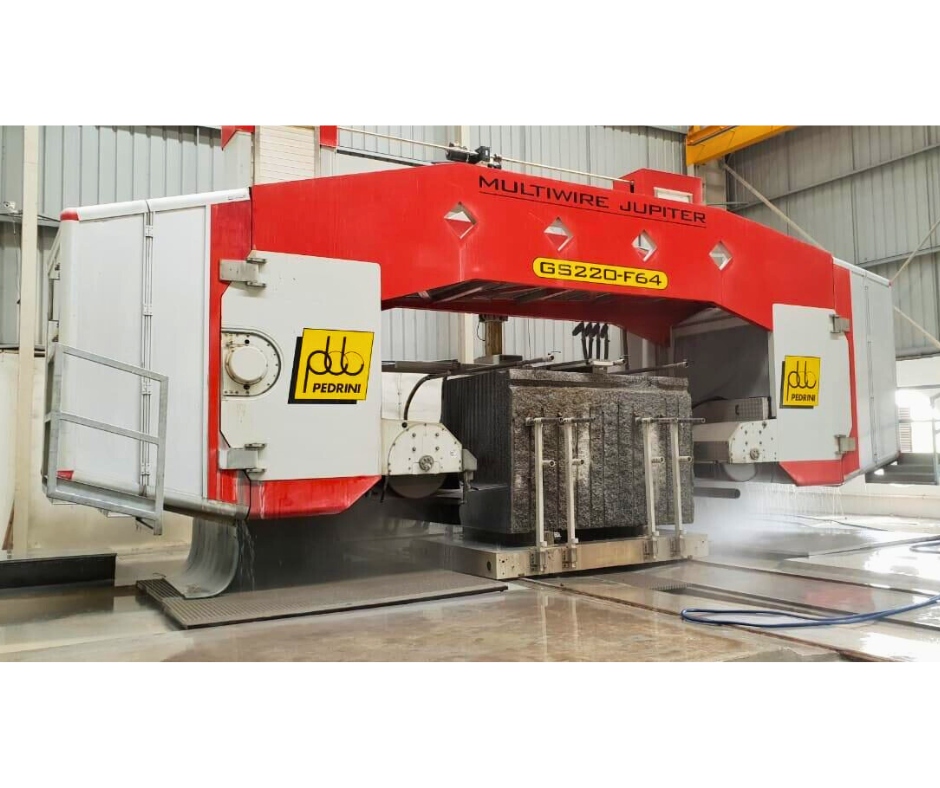
2. Multi-Block Cutter
The multi-block cutter, equipped with up to nine diamond circular saw blades, efficiently slices stone blocks into slabs of varying thicknesses. This machine is built with durable steel and cast iron, ensuring stability and precision during the sawing process.
It features advanced components like a linear motion guide and ball screw for quick adjustments. Additionally, the lubrication system reduces maintenance costs and enhances performance, delivering precise cuts with minimal wear and tear.
3. Automatic Slab Polishers
Automatic slab polishers are used to enhance the surface finish of granite slabs. These machines feature platforms where slabs are placed for polishing. The polishing arm moves across the surface, applying a consistent finish.
Modern automatic polishers use advanced technology, allowing free movement of spindles to optimize the area covered on each slab. This not only improves the efficiency of polishing but also reduces costs, enabling granite exporters to maximize the utilization of each slab.
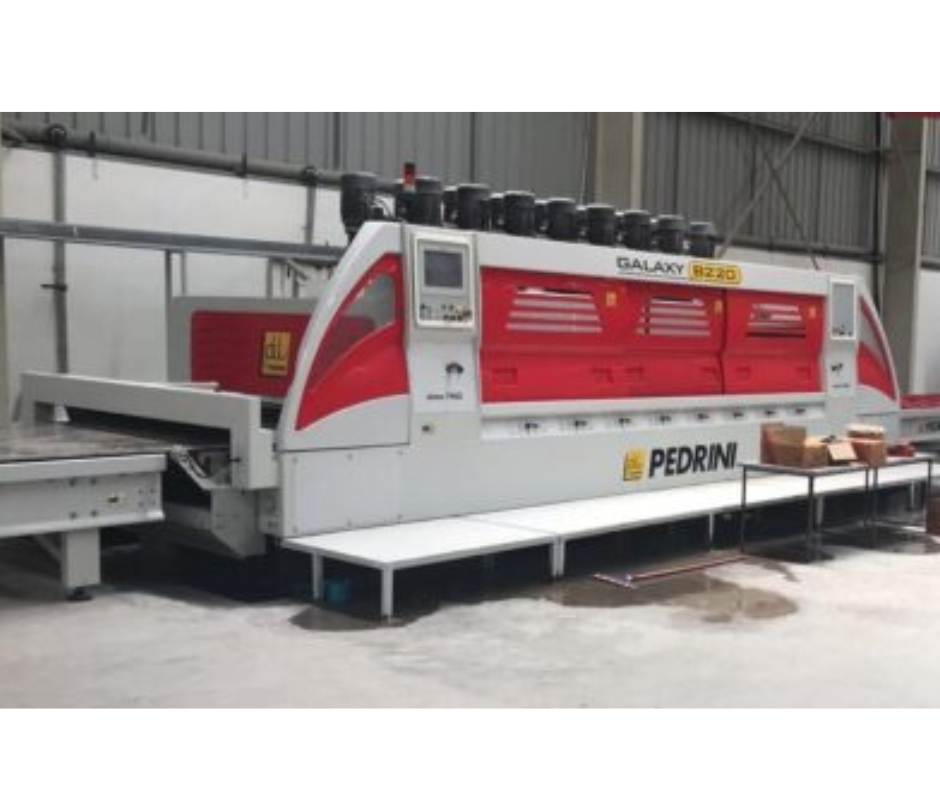
4. Calibration Machine
Calibration machines are critical for ensuring granite slabs and tiles meet exact thickness requirements. These machines feature custom-designed spindles and automated calibrating heads.
They can adjust to different tile sizes without needing frequent changes to diamond tools, making them highly efficient for producing uniformly calibrated tiles. Available in various sizes, these machines provide precise and consistent results.
5. Bridge Cutter
Bridge cutters are essential for processing granite countertops and other custom stone products. This machine uses a water-cooled diamond blade to cut slabs into desired sizes and shapes.
The water cooling prevents the granite from chipping or cracking during the cutting process. Once the slabs are cut, stonemasons use handheld tools to shape and polish the edges, creating a finished product ready for installation.