How to Transport Quartz Slabs Safely: Expert Tips for Damage-Free Delivery
How to Transport Quartz Slabs Transporting quartz slabs can be challenging, even for experienced professionals. Though quartz is durable once installed, it’s surprisingly fragile during transit, and one small mistake can cause chips, cracks, or total breakage—turning a successful project into a costly problem. Since quartz slabs are heavy and rigid with little tolerance for bending or impact, careful handling from factory to site is crucial. To ensure a safe delivery, start by inspecting each slab for flaws and applying protective films. Use sturdy A-frames—made of reinforced wood or metal—and position slabs upright and evenly spaced, secured with non-abrasive straps. Avoid stacking slabs flat, as this increases the risk of stress fractures. Proper labeling, edge cushioning, and avoiding transport during extreme weather further protect the material. Trained handlers, well-maintained vehicles, and trusted shipping partners also play key roles. Whether you’re shipping large batches or a few slabs, these steps will help ensure your quartz arrives in perfect condition.
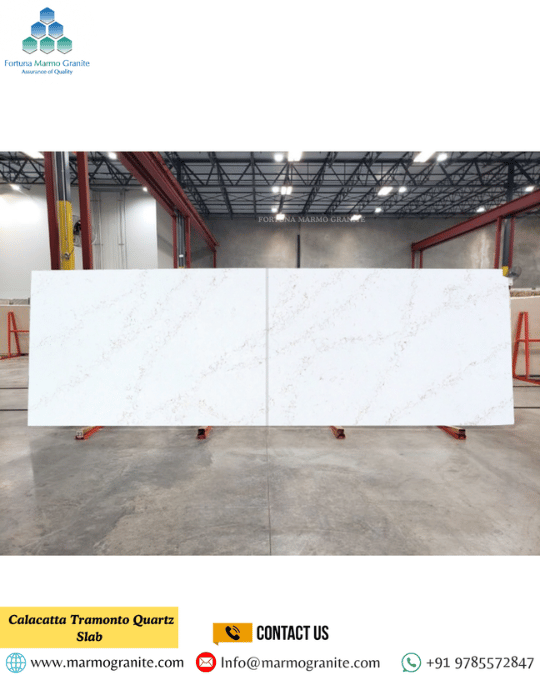
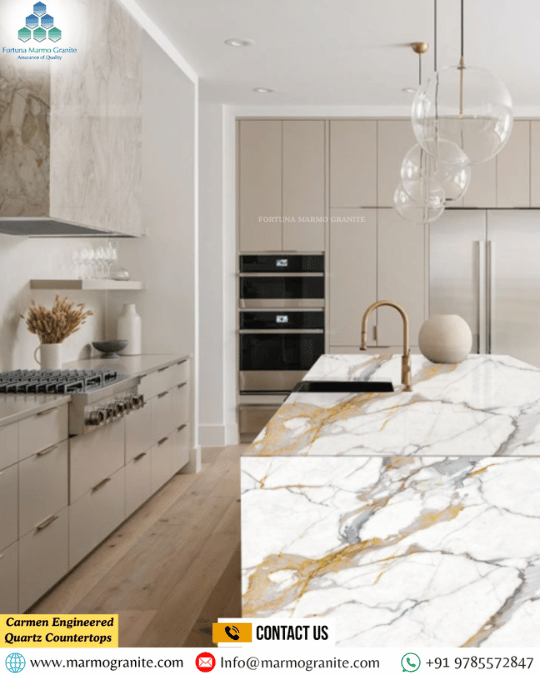
Understanding the Vulnerability of Quartz Slabs
Before learning how to transport quartz slabs safely, it’s essential to understand why extra care is necessary. Quartz is a very hard material (ranking 7 on the Mohs scale), but that hardness also makes it brittle under certain conditions. Unlike flexible materials, quartz slabs have a high modulus of elasticity, which means they don’t bend easily—and when they do, they break.
Here are the key risks to watch for:
- Impact: A sharp hit, especially on the edges or corners, can easily cause chips or cracks.
- Flexing and Bending: Lifting or transporting without proper support can cause the slab to flex beyond its limits, resulting in breakage.
- Vibration: Long rides over rough terrain can loosen fastenings or create tiny cracks that worsen over time.
- Point Pressure: Pressure focused on a small area—like a corner pressing against a hard surface—can crack the slab.
- Thermal Shock: Sudden changes in temperature, though rare during transport, can still cause stress if the slab is exposed to extremes.
The Foundation: Pre-Transportation Checklist
- Slab Inspection: Your First Line of Defense
Before anything else, thoroughly inspect each quartz slab for existing defects. This serves two crucial purposes:
- Documentation: It protects you from liability if damage occurs that was pre-existing. Take clear photographs or videos of any chips, cracks, or imperfections.
- Damage Prevention: It allows you to address any minor issues before they worsen during transit. For instance, a small existing chip might require extra padding in that area.
- Proper Cleaning: A Surprisingly Important Step
Clean the slab thoroughly, removing any dust, debris, or adhesive residue. Not only does this allow for a clear inspection, but it also prevents foreign particles from creating abrasive points against protective materials or causing slippage during handling.
- Edge and Corner Protection: The Most Vulnerable Zones
The edges and corners of a quartz slab are its Achilles’ heel. Even a minor bump can lead to significant damage. Implement robust protection:
- Edge Protectors: Use specialized foam or plastic edge protectors that fit snugly over the slab’s perimeter.
- Corner Guards: Reinforce corners with additional padding or dedicated corner guards.
- Shrink Wrap: Once protectors are in place, tightly shrink-wrap the entire slab. This holds the protectors in place and offers an additional layer of defense against minor abrasions and moisture.
Lifting and Loading: Precision is Paramount
- Choosing the Right Equipment: Safety First
- A-Frames (or Slab Racks): These are indispensable for transporting multiple slabs or a single large slab. They provide stable, vertical support, minimizing flexing. Ensure the A-frame is robust, made of steel, and has a wide, stable base. The contact surfaces should be lined with rubber or a similar non-slip, non-abrasive material.
- Forklifts/Overhead Cranes: For heavy slabs, these are essential. Ensure the lifting attachment (e.g., slab lifter clamps, vacuum lifters) is rated for the slab’s weight and is in good working condition.
- Slab Clamps/Vacuum Lifters: These are designed to securely grip the slab. Regularly inspect their pads for wear and tear, and ensure they have adequate suction or clamping force for the weight.
- Lifting Techniques: Smooth and Controlled
- Always Lift Vertically: Quartz slabs should always be lifted and transported in a vertical or near-vertical position, supported by an A-frame or similar structure. Laying them flat, especially large slabs, can induce significant bending stresses under their own weight.
- Use Proper Lifting Points: If using slab clamps, ensure they are positioned symmetrically and securely. For vacuum lifters, ensure the entire pad makes full contact with the clean slab surface.
- Slow and Steady: Avoid sudden jerks or rapid movements during lifting. Smooth, controlled motions minimize stress on the slab.
- Adequate Manpower: Never underestimate the weight of quartz. For manual handling of smaller slabs, ensure sufficient personnel are present, and everyone understands their role.
- Securing the Slab on the A-Frame
Once the slab is on the A-frame:
- Strap It Down: Use heavy-duty ratchet straps or cam buckle straps to firmly secure the slab(s) to the A-frame. Place padding (e.g., moving blankets, foam) between the straps and the slab’s edges to prevent marking or pressure points.
- Distribute Weight Evenly: If transporting multiple slabs, distribute their weight evenly across the A-frame. Place larger, heavier slabs closer to the center or against the main support.
- Prevent Shifting: Ensure the slabs cannot shift laterally or vertically during transit. Wedges or shims can be used between slabs if necessary, but ensure they are soft and non-abrasive.
On the Road: The Journey to Damage-Free Delivery
- Choosing the Right Vehicle: Stability is Key
- Flatbed Truck/Trailer: For large quantities or oversized slabs, a flatbed truck or trailer equipped with tie-down points and ample space for A-frames is ideal.
- Enclosed Trailer/Van: For smaller quantities or to protect from weather, an enclosed trailer or van can be used, provided it can accommodate the A-frame and secure it properly.
- Suspension Matters: Vehicles with air ride suspension offer a smoother journey, significantly reducing vibrations and impacts transmitted to the cargo. If air ride isn’t available, compensate with extra padding and slower speeds.
- Strategic Loading and Securing the A-Frame
- Center of Gravity: Position the A-frame(s) in the vehicle to maintain a balanced center of gravity. Avoid placing all the weight to one side.
- Secure the A-Frame: This is critical! Use multiple heavy-duty chains or straps to secure the A-frame itself to the truck’s anchor points. Cross-strap for maximum stability. The A-frame must not be able to slide, tip, or shift in any direction.
- Padding Between Slabs (if multiple): If you have multiple slabs on one A-frame, place thin, non-abrasive padding (e.g., corrugated plastic sheets, foam, or felt) between them to prevent rubbing and impact damage from vibration.
- Void Filling: Eliminate any significant voids around the A-frame or individual slabs. Use dunnage bags, wooden bracing, or additional padding to prevent movement.
- Driving Considerations: The Human Element
Even with the best preparation, the driver plays a pivotal role in damage prevention.
- Smooth Acceleration and Braking: Avoid sudden starts and stops. Gradual acceleration and controlled braking minimize forward and backward shifts.
- Gentle Cornering: Take corners slowly and wide, preventing centrifugal forces from pushing the slabs against the restraints.
- Awareness of Road Conditions: Anticipate bumps, potholes, and rough terrain. Slow down significantly before hitting them. If possible, choose routes with smoother roads.
- Regular Checks: For longer journeys, pull over periodically (safely!) to re-check all straps and tie-downs. Vibrations can cause them to loosen. Re-tighten as necessary.
- Weather Awareness: Protect slabs from rain, snow, or extreme temperatures. While quartz is durable, prolonged exposure to moisture during transport can lead to issues with packaging or even the material if not properly sealed.
Arrival and Offloading: The Final Frontier
- Site Assessment: Planning the Offload
- Clear the Area: Ensure the offloading zone is clear of obstacles, debris, and other personnel.
- Level Ground: Choose a flat, stable, and level surface for offloading. Uneven ground increases the risk of tipping.
- Accessibility: Ensure the vehicle has clear, unhindered access to the offloading point.
- Controlled Offloading: Reverse the Process
- Remove Securing Straps (Carefully): Only remove the securing straps and chains holding the A-frame after the vehicle is parked, stabilized, and ready for offloading.
- Utilize Proper Equipment: Use the same lifting equipment (forklift, crane, slab clamps) and techniques used for loading.
- Maintain Verticality: Continue to keep the slabs in a vertical position.
- Adequate Support: Once offloaded, immediately place the A-frame (with slabs still secured) on a stable surface.
Conclusion
Transporting quartz slabs safely is a task that demands meticulous attention to detail, professional handling, and the right logistical strategy to avoid any form of damage during transit. How to Transport Quartz Slabs , while durable once installed, can be vulnerable to cracking, chipping, or breaking if not transported correctly. The process begins with selecting sturdy A-frames designed specifically for stone slabs, using thick padding and edge protectors to prevent impact damage, and ensuring the slabs are secured firmly using heavy-duty straps without exerting excess pressure. Slabs should never be stacked flat, as this increases the risk of breakage; instead, they should be positioned vertically and evenly spaced to distribute weight properly. How to Transport Quartz Slabs Moreover, weather conditions and route planning should also be taken into account, especially when dealing with long-distance transportation, to mitigate risks from moisture, vibration, or sudden stops. Choosing trained handlers and experienced logistics partners is essential, as improper loading or unloading can compromise even the best-packaged shipment. Indian Granite Supplier At Fortuna Marmo Granite, we bring years of expertise in natural and engineered stone logistics, ensuring every quartz slab is packed with precision, protected using industry-approved methods, and delivered to our clients around the globe in flawless condition. Our dedicated team supervises the entire process—from warehouse to delivery site—providing peace of mind and a damage-free experience every time. With a strong commitment to quality, safety, and customer satisfaction, Fortuna Marmo Granite remains a trusted name in the global supply of premium quartz and natural stone surfaces.