Granite Packaging for Export: How Indian Suppliers Ensure Safe Global Delivery
Granite Packaging for Export India plays a major role in the global granite market. Known for its rich variety of stunning natural stones—from the shimmering Black Galaxy to the warm tones of Tan Brown—Indian granite is used in projects all over the world. Whether it’s a towering monument or a cozy home, Indian granite adds beauty and durability. But getting these heavy, valuable stones from quarries to international destinations isn’t simple. It takes careful planning, smart logistics, and most importantly—strong, reliable packaging. Over the years, Indian suppliers have perfected the art of safe granite export. It all starts at the factory, where each slab or tile is carefully checked for quality. Stones are sorted by size, thickness, and finish to make sure everything matches perfectly. Then comes the packing process—and that’s where the real care begins. Each shipment is packed in strong wooden crates, which are treated to meet international shipping standards. Inside, protective materials like foam sheets, plastic wraps, and thermocol keep the granite safe from moisture, scratches, and breakage.
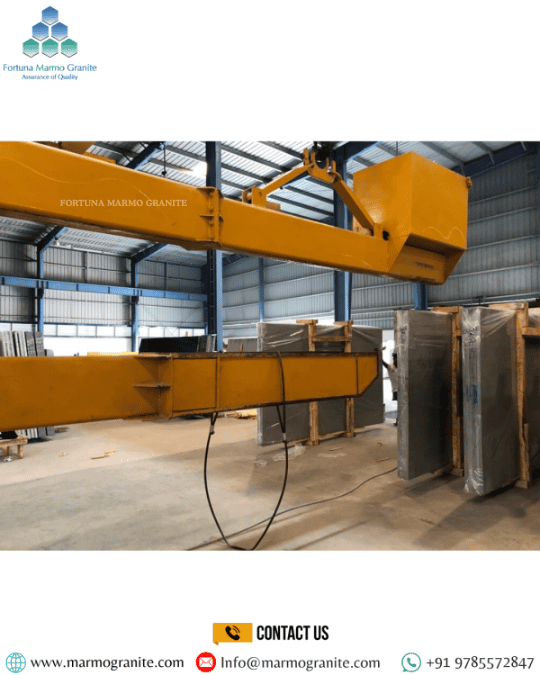
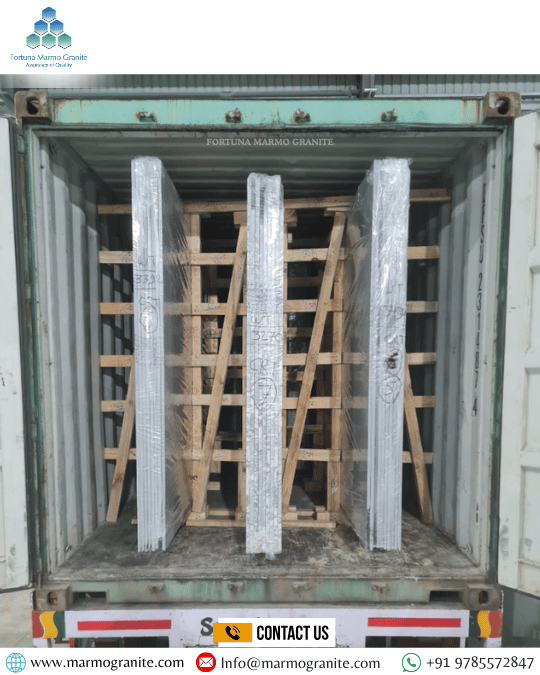
The Imperative of Impeccable Packaging: Why It Matters So Much
Granite is strong—but that doesn’t mean it’s easy to ship. Because of its heavy weight and brittle edges, granite can crack, chip, or scratch if not handled with care. Even a small mistake in packaging can lead to serious damage, which means unhappy customers, rejected deliveries, and costly losses.For Indian exporters like Fortuna Marmo Granite, where large shipments travel across continents, safe packaging isn’t just important—it’s absolutely essential.
To make sure every slab and tile arrives in perfect condition, suppliers use advanced packaging techniques. Each stone is placed in a reinforced wooden crate. Inside, layers of foam, edge protectors, and moisture-resistant wraps keep the granite safe from bumps, friction, and water exposure. Heavy-duty strapping systems lock everything in place, preventing movement during transport.
When it comes to shipping granite, good packaging does more than just look neat. It plays a critical role in protecting the stone and ensuring it reaches its destination safely. Here’s what proper granite packaging is designed to achieve:
- Protection from Damage:
Granite can chip, crack, or scratch during loading, unloading, or transport. Strong packaging helps absorb impacts and reduces the risk of surface damage. - Shielding from the Environment:
Moisture, humidity, dust, and even temperature changes can affect the look and quality of the stone. Packaging keeps these elements out, preserving the stone’s finish.
The Indian Approach to Granite Packaging: A Multi-Layered Shield
1.Wooden Crates and Pallets: The Foundation of Granite Protection
Wooden packaging is the backbone of safe granite export. Indian suppliers like Fortuna Marmo Granite use strong, export-grade, fumigated wood to craft durable crates and pallets that can withstand the heavy weight and rough conditions of international shipping.
For large slabs, A-frames and L-frames are used to hold them vertically. These frames save space in containers and offer excellent stability. Slabs are wrapped in foam or plastic and secured with steel or wooden straps. Sometimes, slabs are packed horizontally on heavy-duty wooden pallets with added shock-absorbing reinforcements.
For tiles and smaller granite pieces, suppliers use robust wooden crates. These crates are reinforced to handle pressure and prevent breakage. Each tile is carefully packed to avoid scratches or chips. This sturdy wooden packaging ensures that every piece of granite—whether large or small—reaches its destination safely, maintaining its quality and beauty for customers across the globe.
2. Smart Cushioning and Surface Protection for Granite Shipping
Indian granite exporters use advanced cushioning methods to ensure each slab or tile reaches its destination safely. Beyond strong wooden crates, they apply smart layers of protection to prevent scratches, chips, and cracks during transit.
First, each slab is wrapped in plastic to guard against moisture and dust. Foam sheets are placed between the slabs to reduce friction and cushion any impact. To protect vulnerable edges and corners, exporters add rubber bumpers, foam corner guards, or reinforced wooden supports.
Shrink wrapping is applied over the packed crates for extra moisture resistance, while heavy-duty steel or plastic strapping keeps everything securely in place. Inside the crates, slabs are further separated using foam or cardboard sheets to avoid surface damage from rubbing. These thoughtful packaging techniques reflect the exporter’s commitment to quality. They ensure the granite arrives in excellent condition—ready to impress, install, and last for years to come.
Quality Control and International Compliance
The commitment to safe global delivery extends beyond packaging. Indian suppliers integrate stringent quality control measures throughout the entire process, from quarrying to final packing.
- Pre-Packaging Inspection: Before any granite is packed, it undergoes rigorous inspection for any defects, cracks, or inconsistencies. Only top-quality materials are cleared for export.
- Adherence to International Standards: Indian exporters strictly adhere to international packaging standards, notably ISPM-15 (International Standards for Phytosanitary Measures No. 15). This regulation mandates that all solid wood packaging materials used in international trade be heat-treated or fumigated and stamped with an approved mark. This prevents the spread of pests and diseases, ensuring smooth customs clearance globally.
- Weight Marking and Load Distribution: Each crate or bundle is clearly labeled with its net and gross weight. This is crucial for preventing overloading of containers and ensuring proper load distribution, which is vital for the safety of the cargo and the transportation vessel.
The Logistics of Granite Export: From Factory to Port
The journey of packed granite from the factory to the destination port involves a well-coordinated logistical chain.
- Optimized Container Stuffing: Indian suppliers are adept at optimizing container space. For slabs, the finished side of each slab is strategically positioned to face each other, minimizing friction. Air gaps between slabs are meticulously eliminated to reduce movement.
- Secure Anchoring: Once packed inside the container, wooden crates and bundles are firmly anchored using wooden frames, chocks, and strapping. This prevents any shifting, toppling, or movement during the entire sea voyage, especially through rough waters.
- Collaboration with Freight Forwarders: Reputable Indian granite exporters partner with experienced freight forwarders specializing in heavy cargo and natural stone. These logistics partners play a crucial role in managing customs clearance, documentation, and ensuring efficient shipping routes.
Labeling and Documentation: The Unsung Heroes
Every crate or pallet is clearly labeled with essential information, including:
- Material Name: Specific granite type (e.g., Black Galaxy, Kashmir White).
- Dimensions: Exact tile or slab sizes.
- Quantity: Total pieces and area coverage.
- Block/Batch Number: For traceability back to the quarry.
- Surface Finish: Polished, flamed, honed, etc.
- Crate Numbering: Sequential numbering for multi-crate shipments.
- Weight: Net and gross weight per crate.
- Client Reference: Purchase order number or project name.
- Country of Origin: “Made in India.”
- Handling Symbols: Standard international symbols like “Fragile,” “Keep Dry,” “This Side Up.”
- Fumigation Stamp (ISPM-15): The crucial IPPC stamp for compliant wooden packaging.
Conclusion
Indian Granite Supplier Granite Packaging for Export is not merely a logistical step—it is a critical safeguard that ensures the product’s journey from the quarry to the customer is smooth, secure, and damage-free. With granite being a dense and often brittle material, the risk of chipping, cracking, or surface abrasion during transport is significant if not handled with precision. Indian suppliers have risen to this challenge with sophisticated, well-engineered packaging strategies that include multiple layers of protection such as plastic sheets, foam cushioning, edge guards, thermocol lining, moisture-proof covers, and heavy-duty wooden crates that are fumigated and ISPM-certified for international compliance. Special attention is given to securing the slabs and tiles so that there is no unnecessary movement during loading, unloading, or transit, whether by sea or land. Strapping systems and forklift-friendly crate designs add another layer of efficiency and safety. Labels detailing stone type, dimensions, destination, and handling instructions are also meticulously added to assist customs clearance and warehouse organization upon arrival. Granite Packaging for Export At Fortuna Marmo Granite, we go beyond just delivering granite—we deliver peace of mind. Our team understands that every consignment reflects not just the value of natural stone, but the reputation of the supplier and the trust of the buyer. With a commitment to excellence and a dedication to perfection, our packaging processes are aligned with global best practices to ensure that every piece of granite—whether destined for countertops, flooring, or monumental architecture—arrives in flawless condition, ready to elevate any space it touches. As a leading Indian granite exporter, Fortuna Marmo Granite combines world-class packaging with dependable shipping logistics, offering clients across the globe a seamless experience from order placement to final delivery, reaffirming our position as a preferred and reliable partner in the natural stone industry.